Norwich, United Kingdom
December 18, 2019
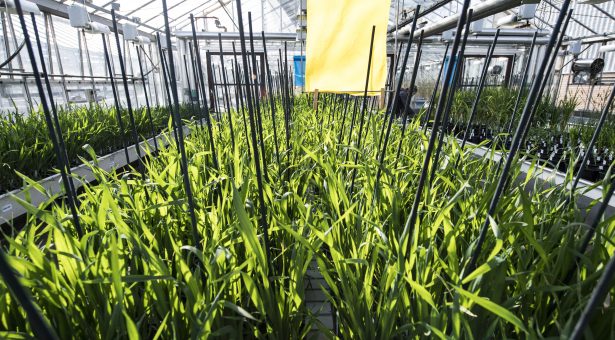
At the John Innes Centre we have 70 Controlled Environment Rooms and glasshouses, where over 7,000 plants are grown each year.
All 7,000 are planted and looked after by our Horticultural Services team.
We took a tour of the glasshouses with our Head of Horticultural Services John Lord to find out why world-class plant science requires world-class horticultural services. First, we wanted to find out about his passionate dislike of hoses.
“In an ideal world I would ban hoses, they just cannot offer a precise or consistent amount of water. They’re not efficient, they’re not economical and they’re not effective.
My background is in horticulture, but I have always been passionate about change management and that was what brought me to the John Innes Centre.
When I first came here a few years ago, I saw a huge opportunity to create a world-class horticultural service. After all, world-class plant science, deserves world-class plants and that’s what we strive to provide. World-class plants for world-class scientists. For that to happen we needed a revolution. Thanks to my team that’s now well-underway.
Good horticulture relies on a lot of variables being right; seed quality, compost, water, daylight, temperature etc. Growing high-quality, consistent crops, means ensuring that every single one of those variables is as effective, efficient and economical as possible. It always comes back to those three E’s; effective, efficient, economical.
Take potting for example. When I arrived here, we had a system whereby each pot was filled by hand. Not only did that mean you had highly-skilled horticulturists spending their time filling pots, but you also had hugely inefficient and ineffective pots.
Why? If you have a tray of 20 pots to fill, you take a shovelful of compost and drop that into the middle of the tray, before spreading it out to fill the outer pots. Once that’s done, you will have 20 pots that look the same, but the ones in the middle will have suffered from soil compaction when the bulk of compost was dropped onto them. This affects both the roots of the plants that grow in them, and how much water they need.
To solve this, we have invested in an automated potting machine to consistently fill pots, ready for planting. The machine requires careful calibration, this is where Alberto Ferreto a specialist in this area comes in. Alberto ensures we offer the best (most effective, efficient and economical) service possible.
Watering is another area where we have made huge improvements to the service we offer. Each plant needs the right amount of water at the right time, it’s crucial to ensuring a healthy, consistent crop. The first step to achieve this is consistent potting, but with the potting machine, the next step is the way you water them.
Top down watering is inefficient and results in more unwanted soil compaction as the water crashes down into the soil. A much more effective and efficient system is to water from beneath, using a system called ebb-and-flow watering. This is a system where each pot sits in a tray that gradually fills up with water at controlled times and to a set depth.
Using ebb-and-flow watering, we can ensure each crop, each plant, receives the same amount of water at the same time. And because it is bottom-up, rather than top-down we reduce the amount of fertiliser lost from the soil, washed away with the excess water.
Pools of water on a glasshouse floor means you have wasted water and fertiliser. It’s not effective, efficient, economical or good for the environment. Ebb-and-flow takes the guesswork away and means we know exactly how much water each plant gets and when. This in turn means we know how much fertiliser that plant has access to.
After potting and watering there is the lighting, which we are in the process of upgrading to LED throughout the glasshouses and controlled-environment rooms.
Dr Brande Wulff’s groups work on speed breeding is well-known and a key component of this is to offer the most effective light for plant growth, we optimise the light that plants use for photosynthesis. Additionally, LED lights produce less heat than the old halogen bulbs, meaning we are better able to regulate the temperature in our glasshouses.
We can now control each light individually, and each one is attached to a sensor, ensuring that the lights are only on when needed. Previously the glasshouse lighting was switched on, on October 1st and that was that for the winter, irrespective of what the weather was doing outside. Now, if it’s a bright, sunny, autumnal day our lights recognise they’re not needed so don’t come on.
All of this ensures we are producing high-quality crops, that are consistent. If you look in one of our glasshouses now, you will see that everything in there is the same height. By standardising the horticulture, you can help standardise the end crop.
The other thing you will notice if you look in one of our greenhouses now, is that not only are the plants all the same height, they’re also all the same species. That might seem obvious, but previously the glasshouses weren’t structured in this way. Instead they operated on a space-to-need basis, in that if there was space in a glasshouse, that’s where you put your plants.
This was inefficient, our glasshouses were operating at about 40% efficiency, and it also creates an ideal haven for pests to move from plant to plant. In glasshouses that were watered by hose, where water splashed over the floor and glass, we were creating exactly the damp, humid conditions pests and diseases thrive in. Investment in the facilities means we can now provide bespoke and distinct areas for each crop.
We now also have a rotation system to ensure each glasshouse is emptied and given a thorough clean between each cycle. Our new system means we can turn a glasshouse around in 24 hours. The other benefit is that this allows for increased specialisation in each area, so for example one of our Horticultural Technicians is Lewis Hollingsworth is our cereals specialist.
We have also brought our crop request system into the 21st Century, by introducing an app through which scientists can order the plants they need, for when they need them. It also provides them with real-time updates on the status and location of the plants, helping to reduce worries and allowing them to concentrate on the science.
In the future we would like to do even more. For example, our current glasshouses were built 40-50 years ago, using the technology available at the time. This means, they contain a lot of metal support structures, which block out light, more than the modern equivalent. Our current glasshouses feature external walls on three-sides making them harder and more expensive to heat and regulate. Some of them even feature drains on the highest point of the floor…
In an ideal world we would build new, larger glasshouses, that are sectioned off and taller. By increasing the volume of air, you make it easier (and more efficient) to regulate temperature.
We would also look to improve the layout and design of the glasshouses. Currently our benches, access and equipment mean about 55% of each glasshouse is available for growth. Improving the design, we could get that up to about 75%.
This would be effective, efficient and economical and that’s at the heart of everything we do; world-class plants for world-class plant science.”